Indore-based Inoflex in expansion mode

Saurabh Doshi started Flexible Packaging xx years ago, with 20 employees in a 4,000 square foot plant. In 2005, Doshi expanded the business and changed its name to Innovative Packaging. Again in 2013, the company revamped its operations and expanded its production capacity and this fourth dimension, Doshi chose Inoflex equally the flagship brand for his flexible packaging concern.
Over the years, Inoflex has grown into i of the biggest flexible packaging suppliers in Key India. "We endeavor not to compromise on the quality of service provided to our customers. I have a thoroughly trained workforce and each one is a specialist in the job he or she does. The packaging supplied undergoes thorough quality checks. Packaging is dispatched to the client but after information technology passes all the quality check criteria," says Doshi, the possessor-director of the visitor.
Currently, Inoflex supplies flexible packaging to major FMCG companies such every bit Tata, Nillons, Yellow Diamond, Patanjali and Marvel Tea. Inside Indore, the company supplies to a huge number of producers and suppliers of FMCG products; and beyond the country to nearly 22 states. It has sales offices in Delhi, Indore and Roorkee a small sales role in the South. Speaking about the implementation of GST, Doshi says, "We are supplying to a huge client base of operations of clients and we had trouble initially. It took companies some time to understand the new taxation regime and settle down with the sharp alter in the billing system. Even so, I must say that GST was an extremely practiced move, i that proved beneficial for us. We have gained new customers afterward the implementation of this regime."
Inoflex to increment production capacity
With 2 production units in Indore, Inoflex tin can produce close to m tons of flexible packaging each month and is currently achieving virtually 750 tons. It is undertaking measures to quickly increment its production at the two factories in Indore. While the smaller plant with a capacity of 300 tons produces packaging for pharmaceutical and food packaging export market, the new constitute on the outskirts of Indore has a monthly capacity of 700 tons which produces mainly for domestic nutrient and confectionary market. In November, the company will initiate the expansion of the new advanced gravure plant with the purchase of a brand new Pelican gravure press.
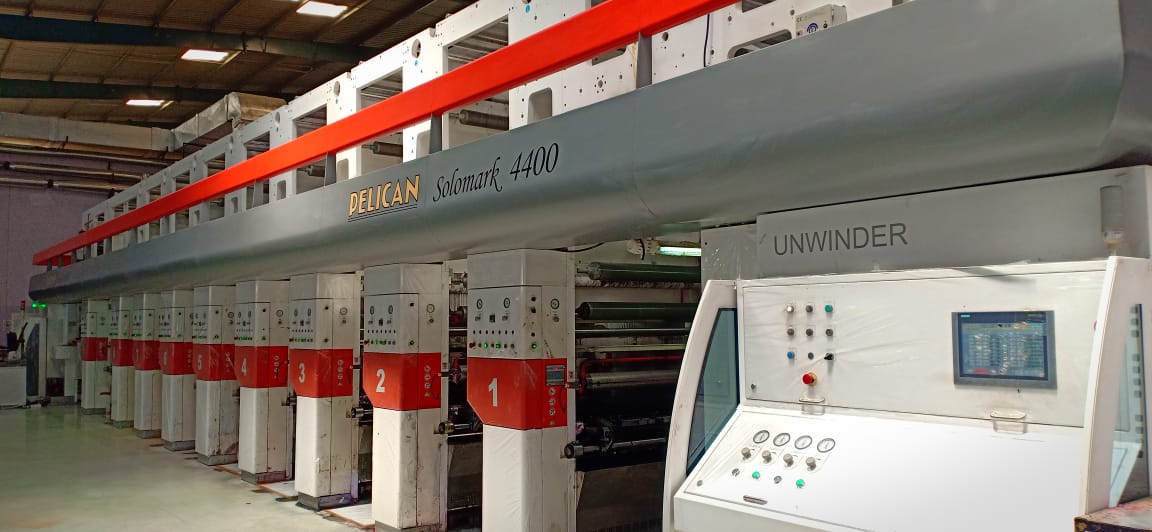
Inoflex on flexo versus gravure
Talking about investing in gravure and CI flexo presses, Doshi explains, "We are also planning to install a CI flexo in the adjacent ii years. CI is still a budding applied science in the Indian market, which is largely dominated by gravure. No doubt CI has grown significantly, merely I retrieve in that location is all the same time for the new engineering science to settle in India. CI is even so to grow beyond diapers, sanitary napkins, milk pouches and the edible oil packaging market."
Whether CI or rotogravure, the main issue is the try to improve the sustainability of flexible packaging by moving to single polymer substrates to make the packaging easier to recycle. "The market place has inverse in the last two years undoubtedly. Ten years ago, of the 100 flexible packaging presses that were coming to India, all 100 or 99 machines were rotogravure. Now, out of 100, at least 90 are rotogravure whereas 10 are CI flexo presses. Going by the trend, I think the scenario five years from at present will exist just the opposite. If yous talk well-nigh the impress quality of both the processes, I retrieve there will e'er be a difference. However today, looking at the irresolute authorities norms and the impact on the surroundings, I call up a time will come when converters will have to change to CI flexo or single family laminates," says Doshi.
Doshi points out that the limitations of CI flexo; toll, barrier property and sealing simultaneously, needs to be eliminated for it to become a more popular or successful technology in the Indian market. Withal, he adds that gravure is unlikely to be eliminated because in Indian conditions the shelf life of gravure impress is unmatched. "Looking at all this, nosotros are adding some other gravure line and will accept fourth dimension before adopting CI flexo," he says.
Major Pelican customer in India
Inoflex has two fully loaded Pelican rotogravure printing presses. "We've not taken the Pelican Ceruti presses yet because they're shaftless and our wide customer base and high number of chore changes with smaller run lengths practice not go far viable. In this scenario, a shafted press is the all-time for u.s.," says Doshi.
Inoflex has two Pelican Solomark presses – an 8-color, 200 meters a infinitesimal press and a 9-color, 400 meters a minute press. Information technology also has iii Pelican laminators, two of which are solvent-less and one solvent-based. In addition, the company has 4 Pelican slitting and rewinding machines.

Inoflex has two 3-layer diddled film lines – a 3-layer, 2.2 meter wide line from Mamta Mechanism and some other iii-layer, ane.2 meter wide line from Windsor. A new Windsor 5-layer diddled film is expected to exist installed soon. "Nosotros were so far working on non-barrier laminates and wanted to expand our product offering in the market and hence have opted for a 5-layer blown pic line," confides Doshi.
"Pelican is a trusted brand. I've been using Pelican for years now and have never faced any problems. Notwithstanding, since we're looking to invest in a faster than 400 meters a minute press, we will take to look at the other options in the market before finalizing our order. Yet, we would as well similar to have all the equipment from the aforementioned family, which makes it easier for u.s.a. to operate in the marketplace. After our adjacent expansion, our monthly product capacity will grow by approximately 300 to 400 tons," says Doshi.
The company also specializes in four-layer laminates and has a co-extrusion motorcar from Fong Kee Extrusions based in Taiwan, U.s.-made dice with a consummate gravimetric dosing system. Commenting about Inoflex'due south delivery towards quality of the product, Doshi says, "I prefer to invest more in my labs than the machines for packaging production as these labs alone can assist the packaging authorize various standards."
Source: https://packagingsouthasia.com/packaging-production/indore-based-inoflex-in-expansion-mode/
0 Response to "Indore-based Inoflex in expansion mode"
Post a Comment